大家對「3D 列印」(3D printing)這個名詞應該並不陌生,不少人以為它是近年興起的新技術,其實不然。
「3D 列印」更正式的名稱為「積層製造」(Additive Manufacturing, AM),意即透過材料層層疊加,製造 3D 立體物件的過程。它早在 20 世紀末便被發明出來,不過當時因價格昂貴且技術門檻高,並未被廣泛利用,直到近年隨著 3D 列印機及線材的成本大幅下降、3D 列印的軟體日趨簡易,3D 列印的應用才開始普及化。
現在,使用者僅需透過一個設計軟體、一台 3D 列印機,便可包辦從設計到製造的所有流程,將一間工作室變為一家 OBM (原創品牌製造商),撤底打破傳統商品產製的藩籬。
3D 列印的技術目前被應用在各個領域,包含航太業、製造業、教育業、軍工業。而其中,3D 列印在醫療產業上的貢獻良多,應用備受注目:如手術前的輔具模型、體外輔具製造,及體內植體製造——也就是台灣新創光宇生醫的專長。
從車庫開始的「植入物」研發之旅
光宇生醫成立於 2017 年,是創辦人陳俊宏第三度創辦的新創公司。陳俊宏為醫學工程及化工背景出生,曾在工研院服務,更是著名的「台灣-史丹福醫療器材產品設計之人才培訓計畫」(Stanford-Taiwan Biomedical Fellowship Program,STB)訪問學者,專業背景及產業經驗都相當堅強,這次創立的光宇生醫更是結合醫療專業及精密 3D 列印技術,立志成為植入式醫材的技術領導者。
「我那時候在矽谷待了快兩年,回台後發現台灣醫療器材製程落後,加上美國剛好 3D 列印蓬勃發展,便開始著手研究。」陳俊宏說道。
他開始在家中鑽研相關技術,就像其他創業者,他的創業雛形也在家中車庫誕生。「我家真的有個車庫喔!」他打趣地說,同時,他在車庫中的開發的技術及潛在商機也吸引了其他創業夥伴加入,團隊成員包含美國柏克萊大學、美國麻省理工學院、台灣大學醫學工程所、清華大學化學工程所等國內外名校的頂尖人才,整合來自軟體、硬體、材料與醫療端的專業,並一手包辦研發、製造、商管、法規認證環節,為客戶提供完整的客製化醫材產品解決方案。
何謂「植入物」?
要深入了解光宇生醫,首先得先了解何謂「植入物」。植入物泛指針對特定目的,埋藏在人體裡的醫療裝置,舉凡骨釘、心臟起搏器、人工關節、隆鼻鼻墊、乳房填充物、避孕器等皆屬醫療植入物,就連一般常見的植牙也屬其中一種。「醫療器材中穿戴式的對我們來說並不難,最難的是便植入物,也就是再生醫學的領域」陳俊宏說。而當困難的再生醫學,配上創新的 3D 列印,變成為光宇生醫的亮點所在。
醫療植入物三大痛點:需量產、高成本、規格化
目前市面上的醫療植入物主要面臨三大問題:需量產、高成本、規格化。
傳統生產流程為:設計、開模、打樣測試、製造。每開模一次便是一筆固定成本,為了極小化成本、極大化收益,產品必須大量生產來降低單位生產成本。然而,相較於其他日常用品,因醫療植入物客群小,市場需求數量低,生產成本相對提高,成為醫療器材廠投入研發醫療植入物的一大阻力。加上醫療植入物通常置架期時間有限,不利於庫存囤放,因此不宜一次大量購入,由此可見量產思維並不符合醫療植入物的特性。
因醫療植入物與人體安全息息相關,僅能使用通過醫療認證的原料,高品質原料自然也大幅提升了材料成本。除了材料本身高單價外,傳統的製造方法常透過切除多餘原料,以「減法工藝 」製造產品,這無形中也造成許多高成本材料的浪費,十分可惜。
最後,量產思維無法提供客製化服務。因醫療植入物會放入人體體內,而每個顧客生理構造不盡相同,規格化的植入物僅能「大致」符合病患需求,難以達到最符合每位病患的理想狀態。舉例而言,小耳症的病患需透過外耳重建來幫助其復健,若僅採用制式化模板,植入後可能無法與對側耳型相似及具有夠深的外耳道,不利於提升患者美觀及自信。
整合醫材及 3D 列印專業,發展客製化解決方案
「醫療器材廠覺得自己有通路不願做這個, 3D 列印廠通常也只做設備,所以我們剛好結合兩者,填補之間的空隙。」光宇生醫看見需求,以 3D 列印技術克服以上困難。首先,3D 列印技術突破了量產思維:透過 3D 列印,產品製造不再需要開模。設計、開模、打樣測試一併透過電腦輔助設計(CAD)軟體便可搞定,大幅縮減固定生產成本,也增加了產品製造的彈性——從下訂單到出貨最多不超過 20 天,需要再訂,無須囤貨。再者, 3D 列印採用採用層層堆疊「加法工藝」製程,大幅省下製造過程中耗費的材料,降低浪費;最後,接到產品規格後,僅需在 CAD 軟體中調整設計便能輸出產品,過程快速、便利,輕鬆滿足客製化需求。
「可吸收的、不可吸收的、不同吸收速度、不同力學考量,放鼻子的、放頭蓋骨的都不一樣,這些靠 3D 列印都能做得到。」陳俊宏提及應用範圍時說道。目前光宇生醫的可植入產品製造服務採 B2B 模式,以專案模式服務客戶。
一條龍商業模式:從材料到成品全部包辦
事實上,光宇生醫不僅製造植入式產品,從原料到製程、材料跟產品,光宇生醫全都包辦。「其實醫療植入物在我們領域並不會太難,但要轉成 3D 列印規格的材料才是重點」然而,光宇生醫已克服最大的難關。光宇生醫於 2017 年成功打造智慧積層製造系統與智慧材料生產系統原型機,並於 2019 年 MeDFila® PCL 全系列材料獲得美國 FDA 之 MAF 證號。有了製造機器、有了製造材料,光宇生醫便能開始針對全身 300 多個地方,製造可吸收植入物,每個植入物都能申請一張認證。「我們像金雞母一樣一直在生蛋,之前窩都做好了,現在就是養雞生蛋、養雞生蛋」陳俊宏表示。
光宇生醫獨特研發的 MeDFila 3D 線材為「高分子與陶瓷混合可降解 3D 列印材料」,除了獲美國 FDA 認證外,公司將販賣單位從「公斤」降為「克」,能避免囤貨造成降解的現象,也能做到少量供應的服務,成為產品一大優勢,更已獲不少歐美客戶採用 。「當顧客成功使用我們的線材,我們便綁定了這個客戶及這條生產線了」陳俊宏說。 MeDFila 目前透過業務窗口進行銷售,或與區域代理商合作,提升產品滲透率。
目標鎖定在「醫材界的台積電」
光宇生醫將持續與馬偕醫院、長庚醫院、史丹佛大學的醫生們合作,目標於 2030 年完成建置醫療及列印系統,並也在尋找供應鏈相關策略性投資者。
「希望以少量、客製、高單價,成為醫材領域的台積電」也成了光宇生醫的願景。
創業快問快答
Q:請簡述貴公司的服務內容?
A: 透過自行開發的積層製作設備與材料做醫療植入產品開發,提供醫療器材商或臨床醫師一個已驗證之積層製作的快速商業化平台。
Q:服務的創意來源,是因為發生甚麼事情而有這樣的想法??
A:目前3D列印在臨床醫療服務端只能進行模型的製作而無法作為真實植入物的工具,主要因為設備與材料大多為國外公司掌握,而創辦團隊本身在植入式材料與高風險醫療器材開發上相當熟悉且精通,因此創辦人在2013在美國訪問研究時,轉念將常見的積層列印設備進行關鍵零組件升級與優化,達到可植入人體之功能,因而拓展了這份事業的開始。
Q:創業,教會了你哪些事?簡單分享創業至今以來的心得感想?
A:1.核心工作團隊成員組成完整,目標一致工作效率高 2. 選擇最佳路徑,而不是最便宜或最快的路徑 3. 選對大方向與大的切入主題
公司資訊
公司名稱:光宇生醫/Advanced Biomedical Technology
成立時間:2017/5/17
產品名稱:積層製作客製化醫療植入物
上線時間:2020/1/1
官方網站|新創資料庫
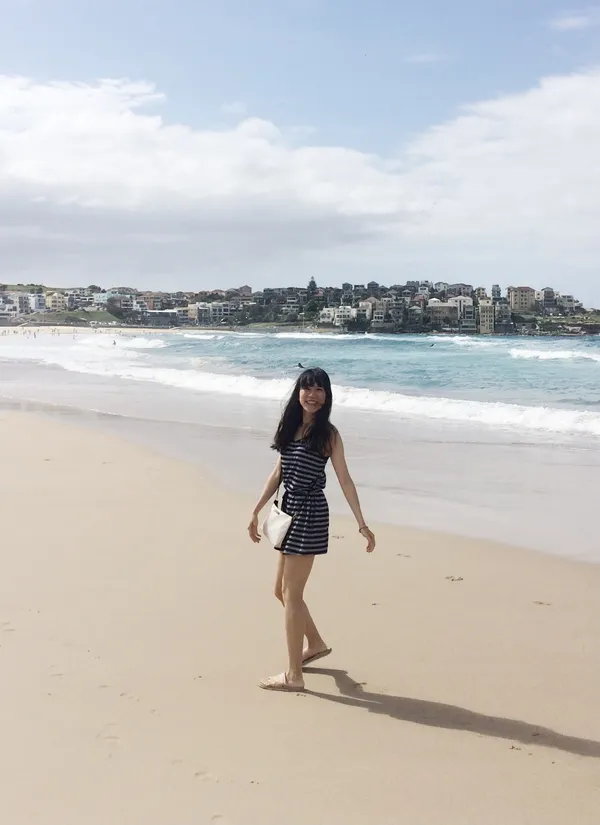
新創團隊採訪請來信:meet@bnext.com.tw
2011年起《數位時代》開始以Meet社群品牌推動創業家們的交流連結。從新創團隊的採訪報導、創業小聚月會的分享、產業沙龍的分享, 提供創新與創業社群相互分享與媒合的平台。